Working with the cellular automata has been fascinating and has opened many possibilities for form and concept, which we've been exploring widely. The files are enormous and the mathematical and formal design work is extremely time consuming. Some of the finished early test pieces are here (one of our new Slip Rabbit cups also makes an appearance in the last photo). The cylinders are 11.5" heigh.
Glaze kilns are out
The new research with cellular automata keeps the studio very busy these days but finally managed to get all of the pieces from the past two months glazed and fired! They are just out of the kiln and photographed on the studio table. There are new Slip Rabbit cups as well. They will be available for purchase during our second Open House on March 17th and on http://quickrabbitdesigns.bigcartel.com/
Web Shop Opens on Bigcartel
We are excited to announce the opening of our sister label's store, the QuickRabbit Designs Web Shop on Bigcartel. QuickRabbit Designs features unique functional, sculptural, and jewelry design objects by Timea.
All sales support the mission of Slip Rabbit programs in digital ceramics and helps us keep our studio open to students, artists residents, and research collaborators.
New Slip Rabbit Logo
Our wonderful graphic designer in residence, Eli Kahn, has designed us a logo that we believe expresses the raison d'etre of Slip Rabbit: Collaboration, Dynamism, and Playfulness.
Two pink rabbits running around in a circle (or turning like spokes around a hub) represents the studio's mission of interdisciplinary research and education, creating partnerships and a welcoming atmosphere of inventing, problem-solving and making, and the role the studio plays by bringing the digital process into the traditional craft of ceramics.
Winter Research Focus: Logic of Things
This week, we have made great advance in two significant areas for printing algorithmic patterns: On one hand, working with mathematician Sara Billey, now we have a way to use cellular automata rules to generate codes for algorithmic patterns. I really appreciated learning from Sara more about the math behind this. It is inspiring to see how beautifully complex systems may be created from using a set of simple rules. On the other hand, we now have a method for turning the code into 3D forms and to apply it as texture on larger forms.
You can find some images below and more on Instagram
Welcoming 2 new interns and research collaborator, Prof. Sara Billey
This January, two new interns joined Slip Rabbit. Daria Micovic is a senior in math and Frida Saucedo is a senior in art at the UW. We are also excited about our collaboration with Professor Billey of UW Math on coding and printing rule based patterns, such as Cellular Automata (CA). We are exploring ways similar to the CA that generate infinite variations of pattern in both 2D and 3D. There are lots of ways to go with this process... In the studio, we had already developed two reliable methods for the application of patterns to forms and created weaving textures with these. This time, we would like to put an emphasis on creating the patterning rules by algorithmic means and learning more about why some of these create order while others unravel in chaos.
Below are some of the patterns.
New photos of Fall Projects
Lagging behind a bit with the finishing of many of our wonderful fall projects. All recent pieces have been on a much larger scale (around 30cm's, appr. 12") with lots of delicate details, taking more time to dry properly and to fit into the firing schedule. These are very unique forms with finishes that are really coming together now.
Goodbye Fall Interns!
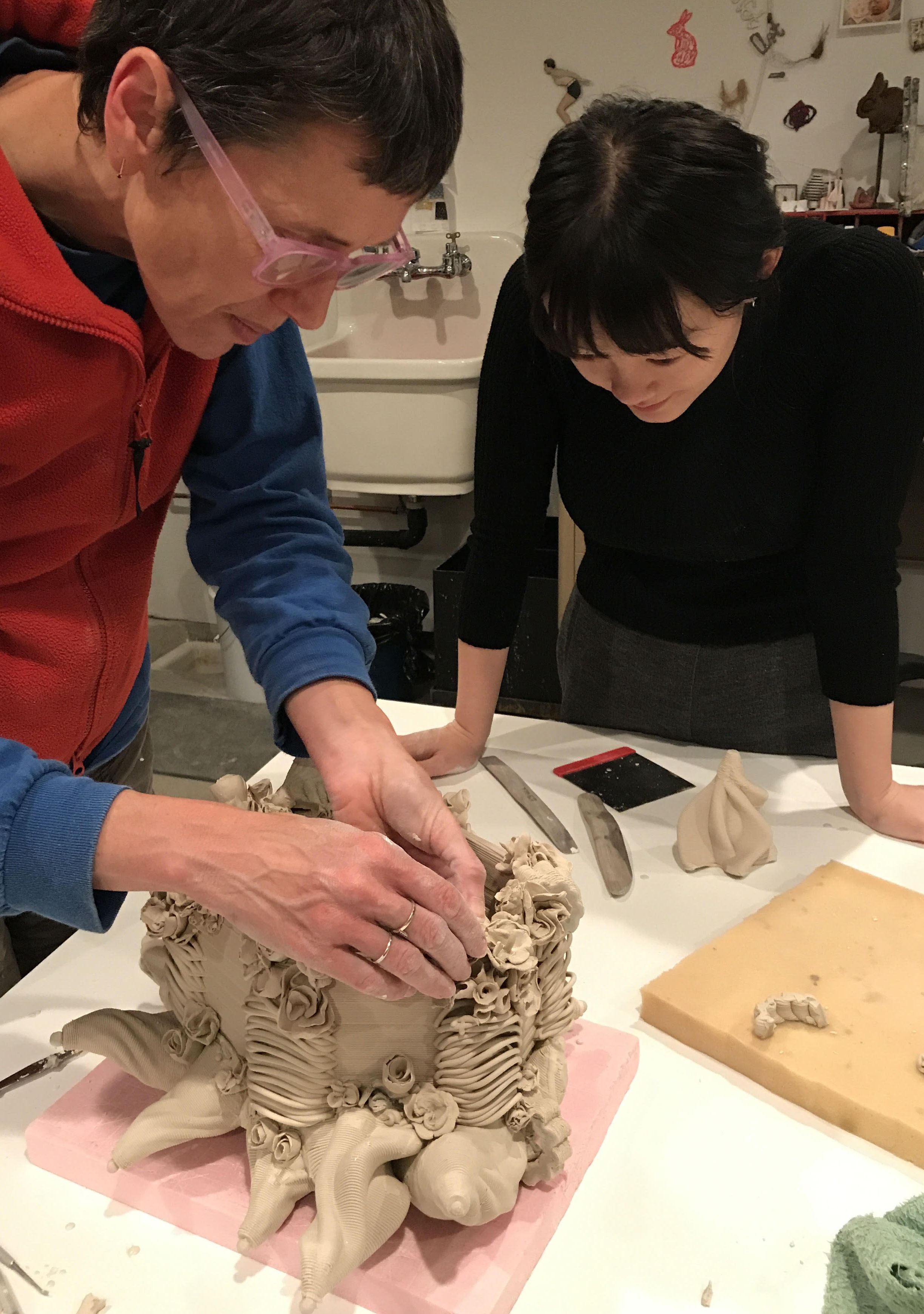
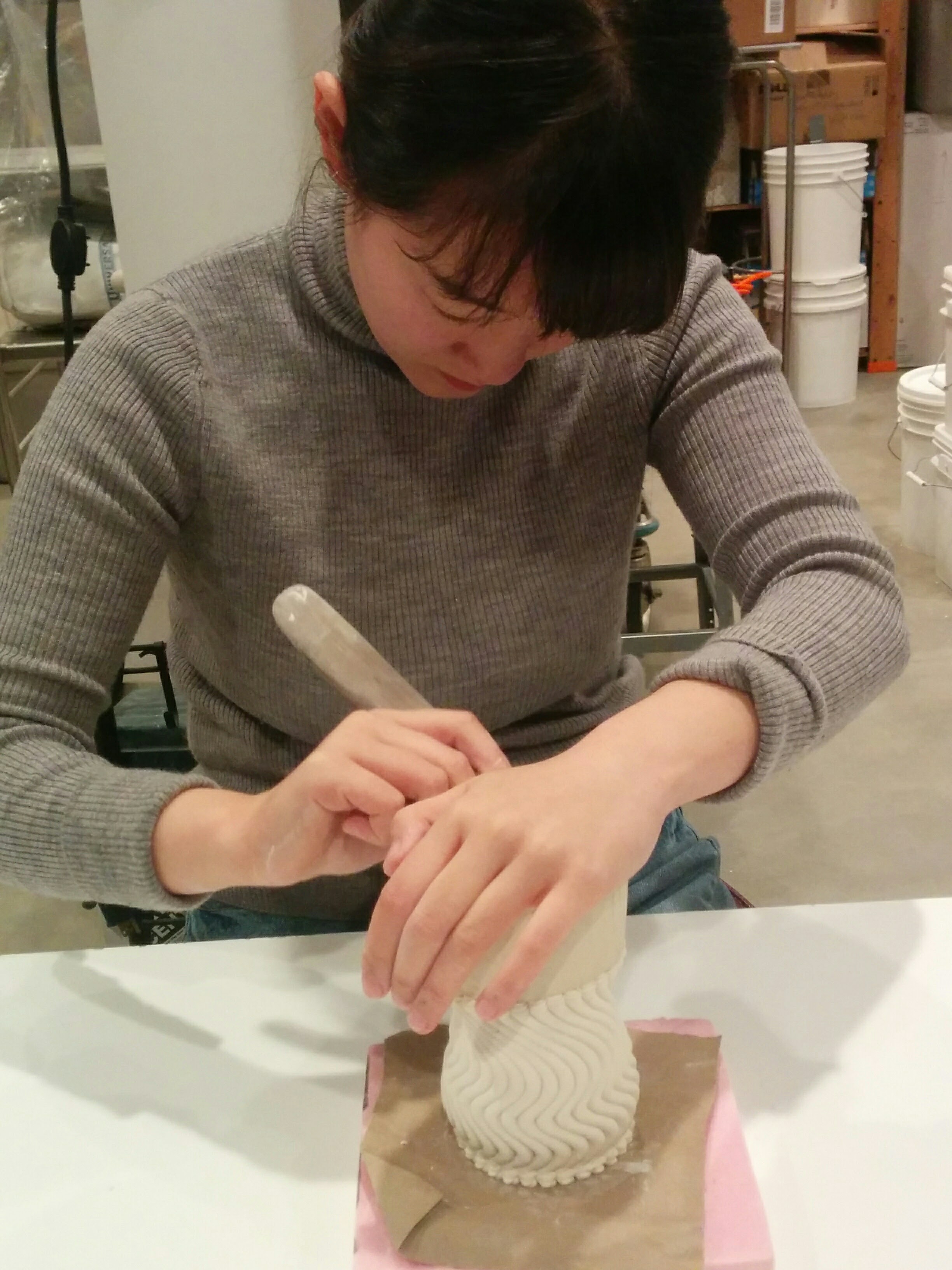

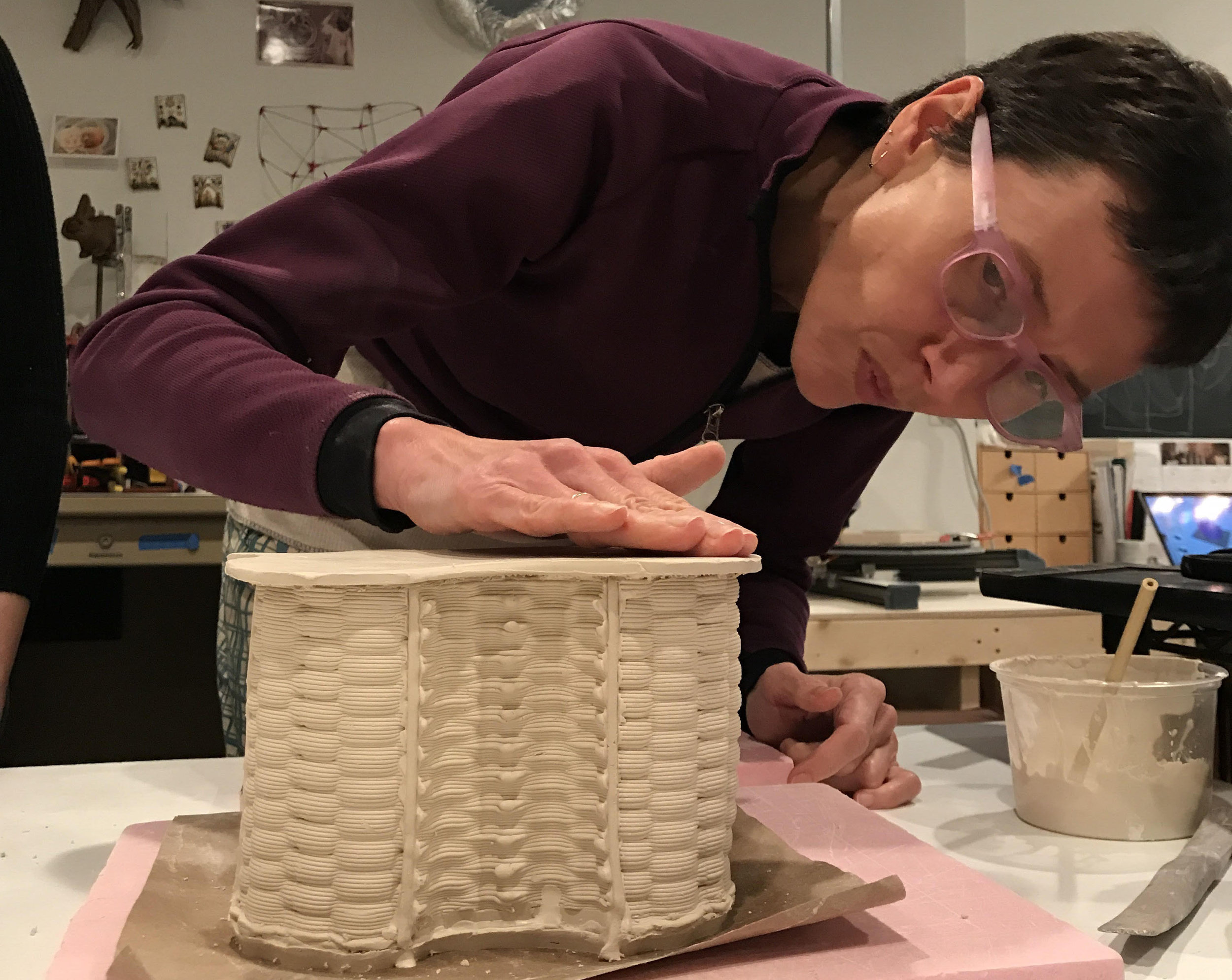
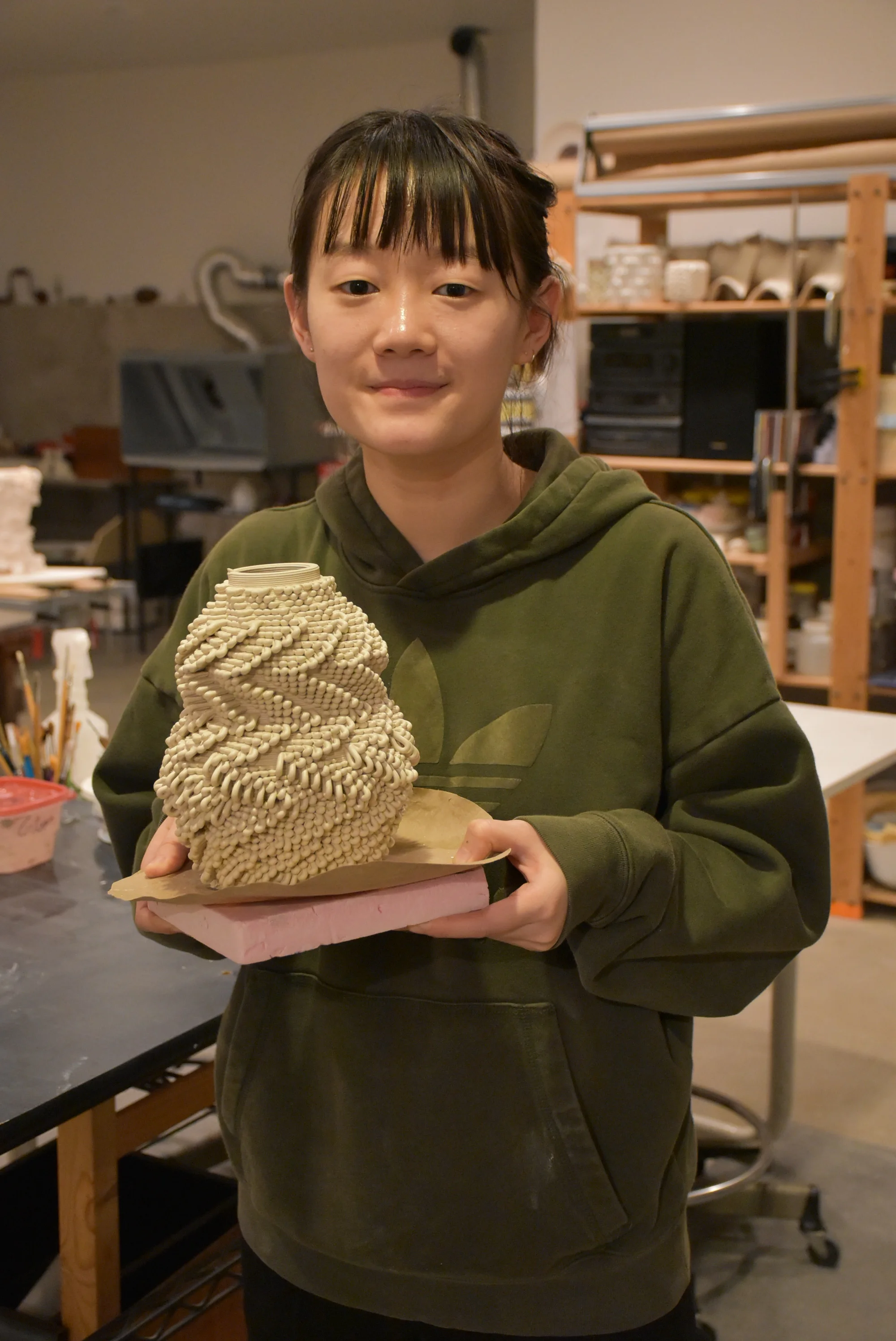
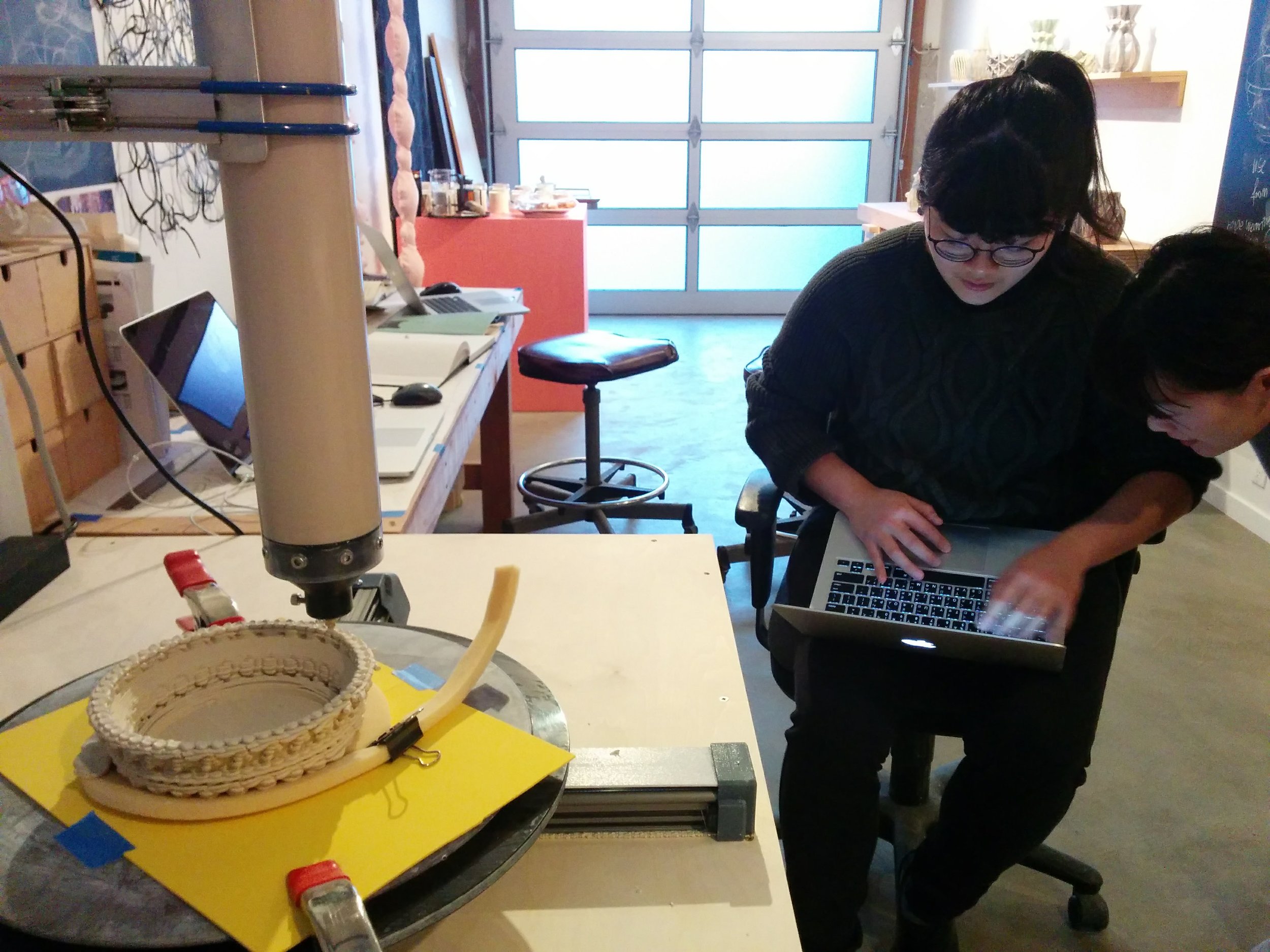
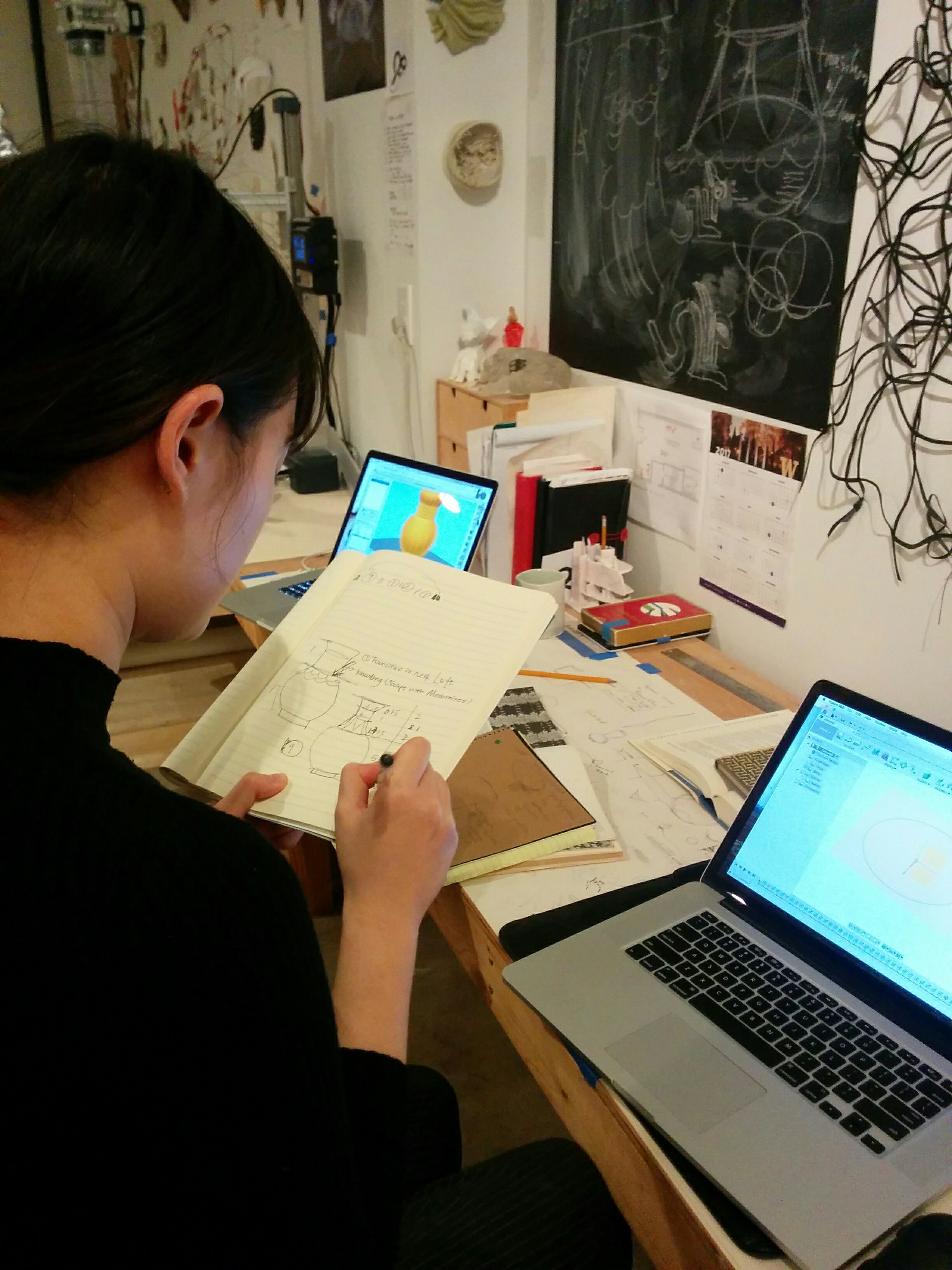
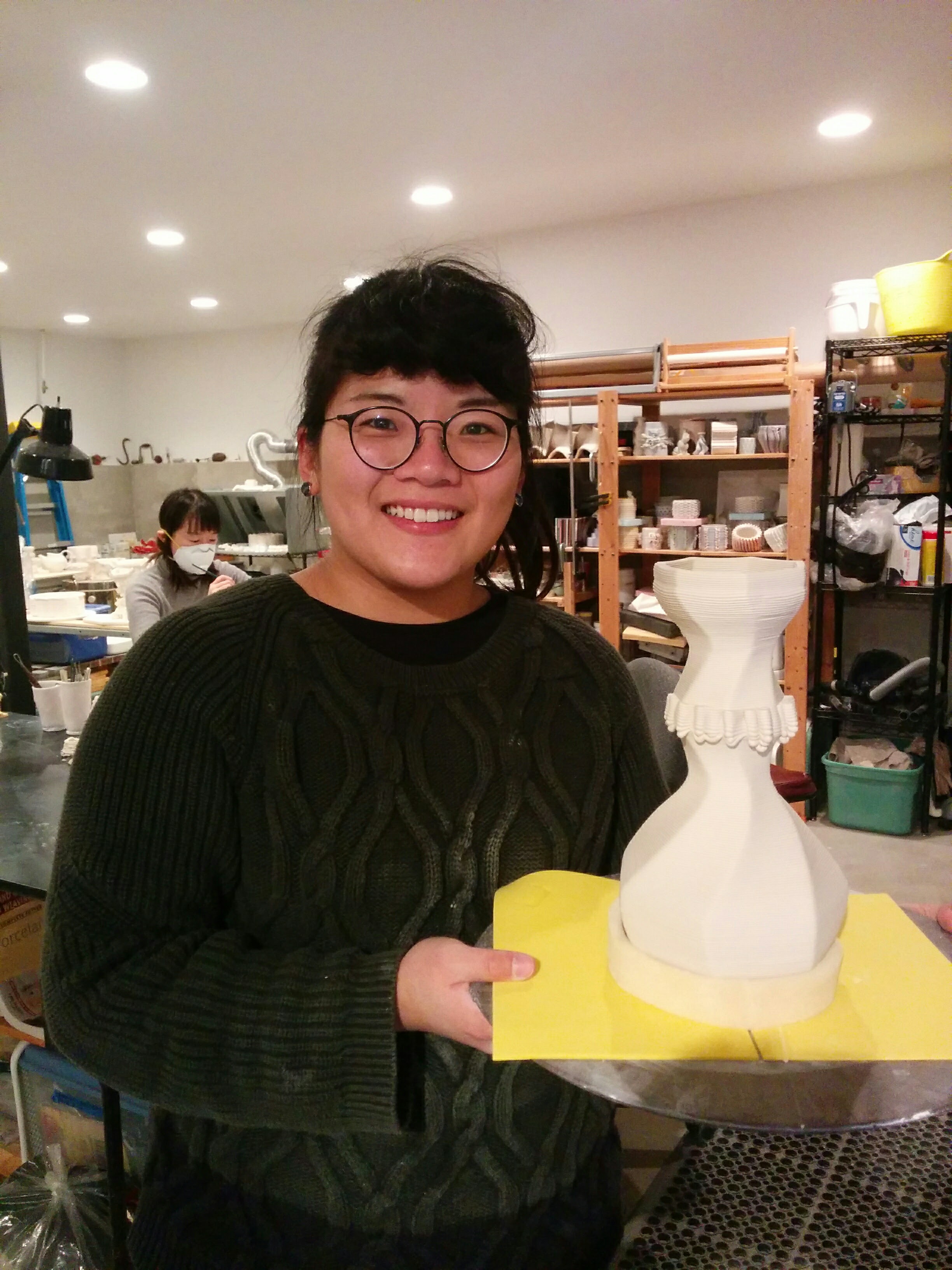
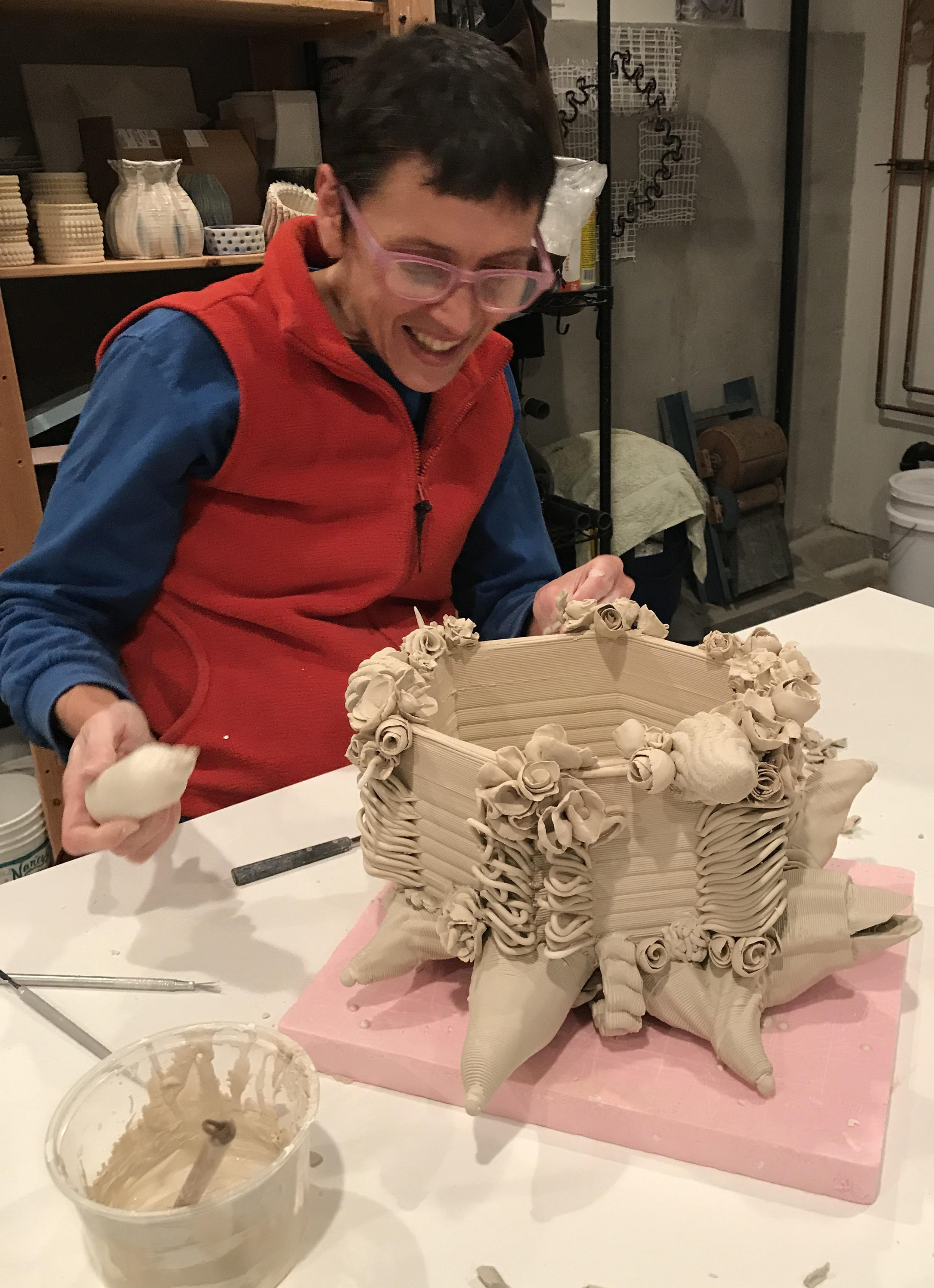
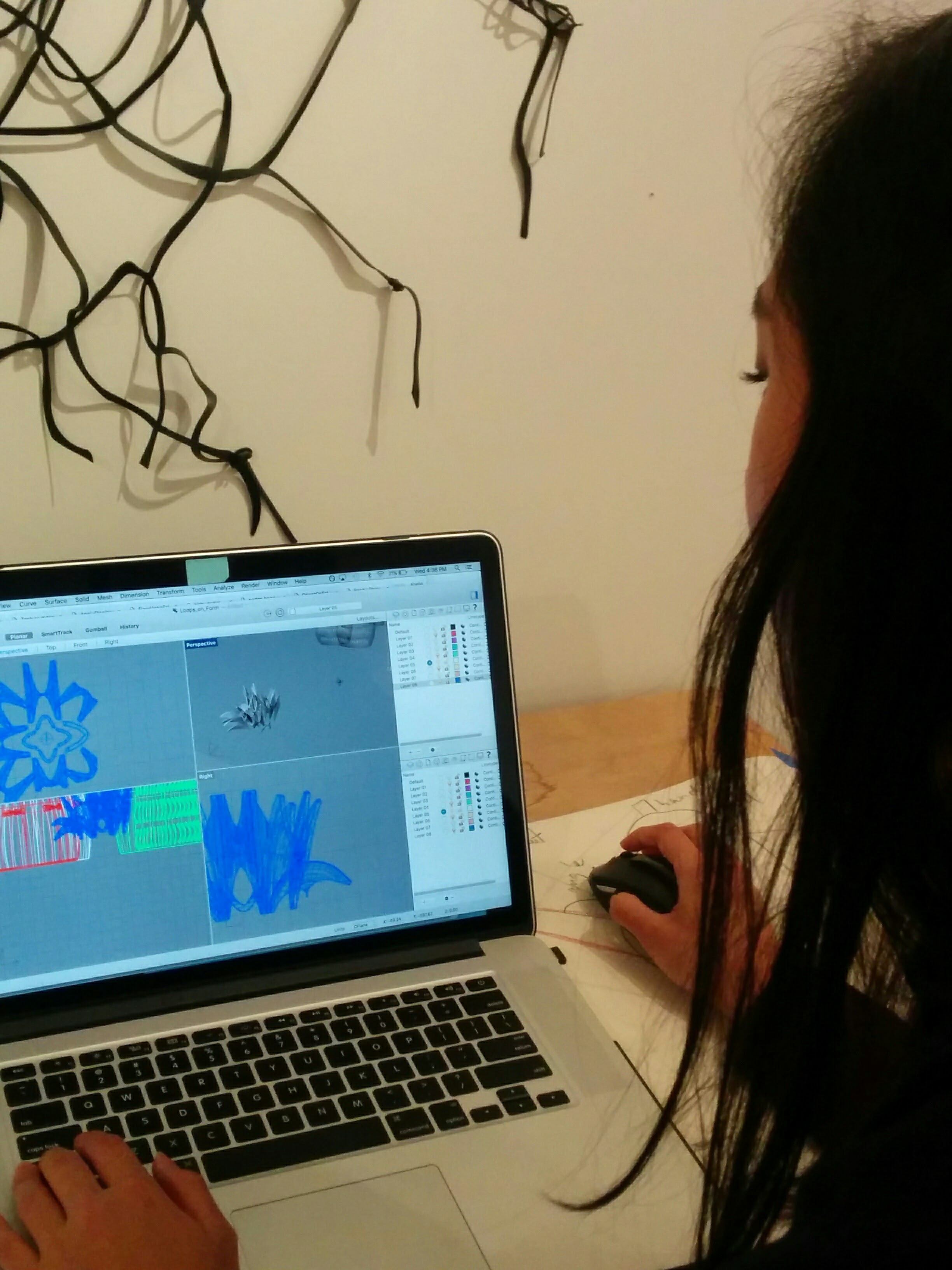

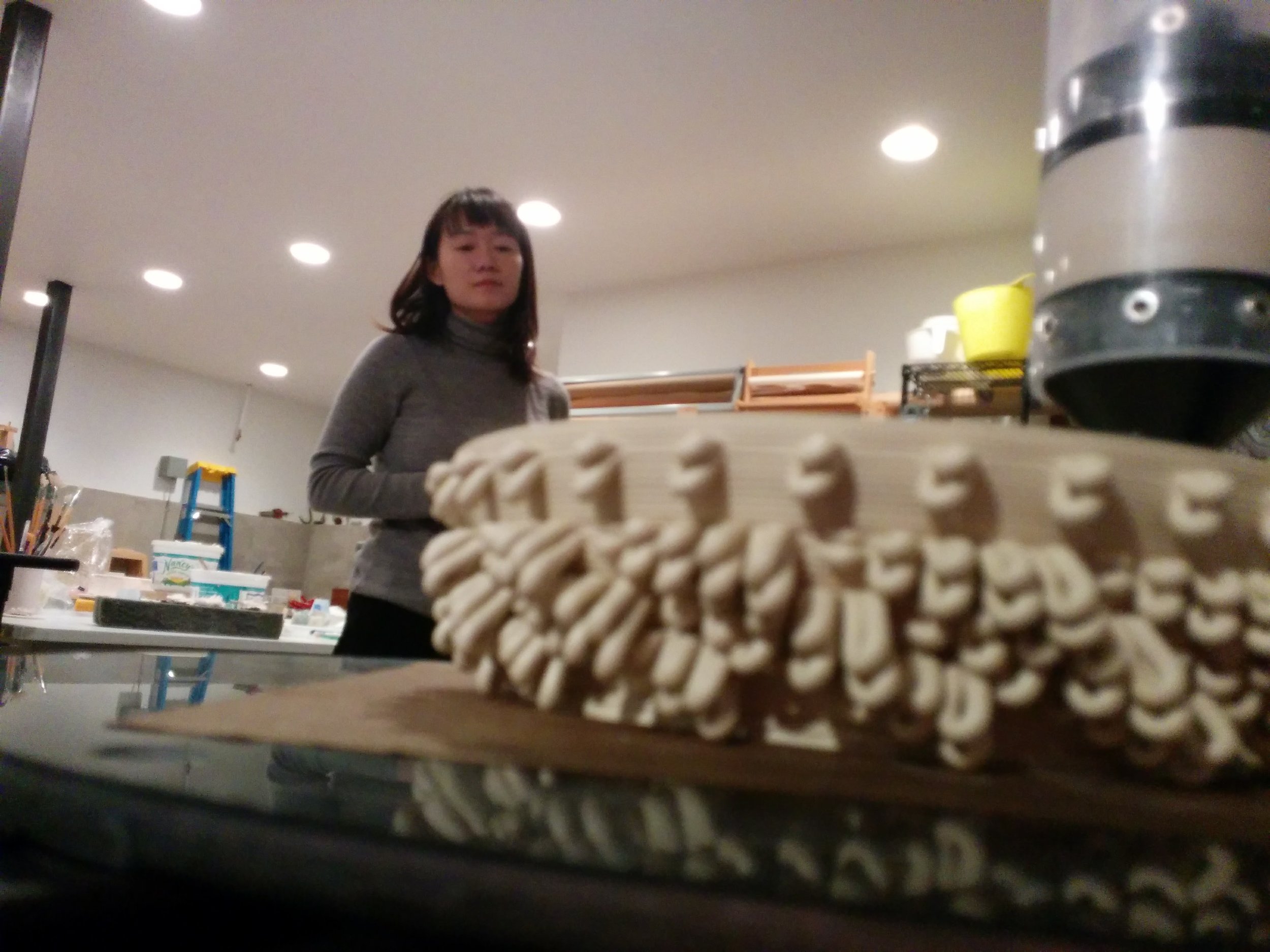
Slip Rabbit interns learn about every aspect of digital ceramics: they gain skills with the software and form design, working with clay and handling the machine and have a chance to create something on their own too.
Three amazing interns are concluding their internship this week. Annabelle, Kate and Qing brought their wonderful exuberance to Slip Rabbit. For the past 3 months (6 for Qing), while plotting and revising designs together, fighting with the CAD software (damn "boolian union"!), tending the print and putting finishing touches on the bisque work we have been chatting and laughing away many hours.
Wishing you great success with your next projects. We will miss you!!
Holiday cheer at Slip Rabbit
The end of the year sneaked up on us. How did we find out? For several weeks now, our studio snack table has been overflowing with cups, each made at the end of printing of the day's worth of work to use up the leftover porcelain in the tube. We love these cups and have amassed a good number of them since the Open House! Their eclectic designs journal the history of our research ideas and the cups themselves also represent each and every wonderful hand that has worked on it, designing, printing, cleaning or painting, and each and every amazing Slip Rabbit intern who has come through the studio.
In addition, and because our team can never-never-ever throw anything away (not even the coil that comes out at priming the printer), printing and clay failures were transformed into jewelry by Timea.
We opened the studio on this past Saturday for a last minute holiday sale. Here are a few pix from that:
Weaving with the clay printer
Our recent experiments with complex loop patterns have also been getting us closer and closer to the ultimate goal of this research chapter: weaving and knotting techniques. After researching numerous sources on basketry, tapestry, on/off loom weaving, crochet, knitting, even macrame (remember macrame?), we've been considering various translations of these into 3D printed textures using our Potterbot7 printer. In many ways, a cylinder is the most ideal form in the first phrase of experimentation, so once again, we've made lots of cylinders. But gradually, as our digital toolkit for the design processes of knots and weaves developed, we’ve also became able to wrap patterns around forms or compose them into larger and more complicated vessels.


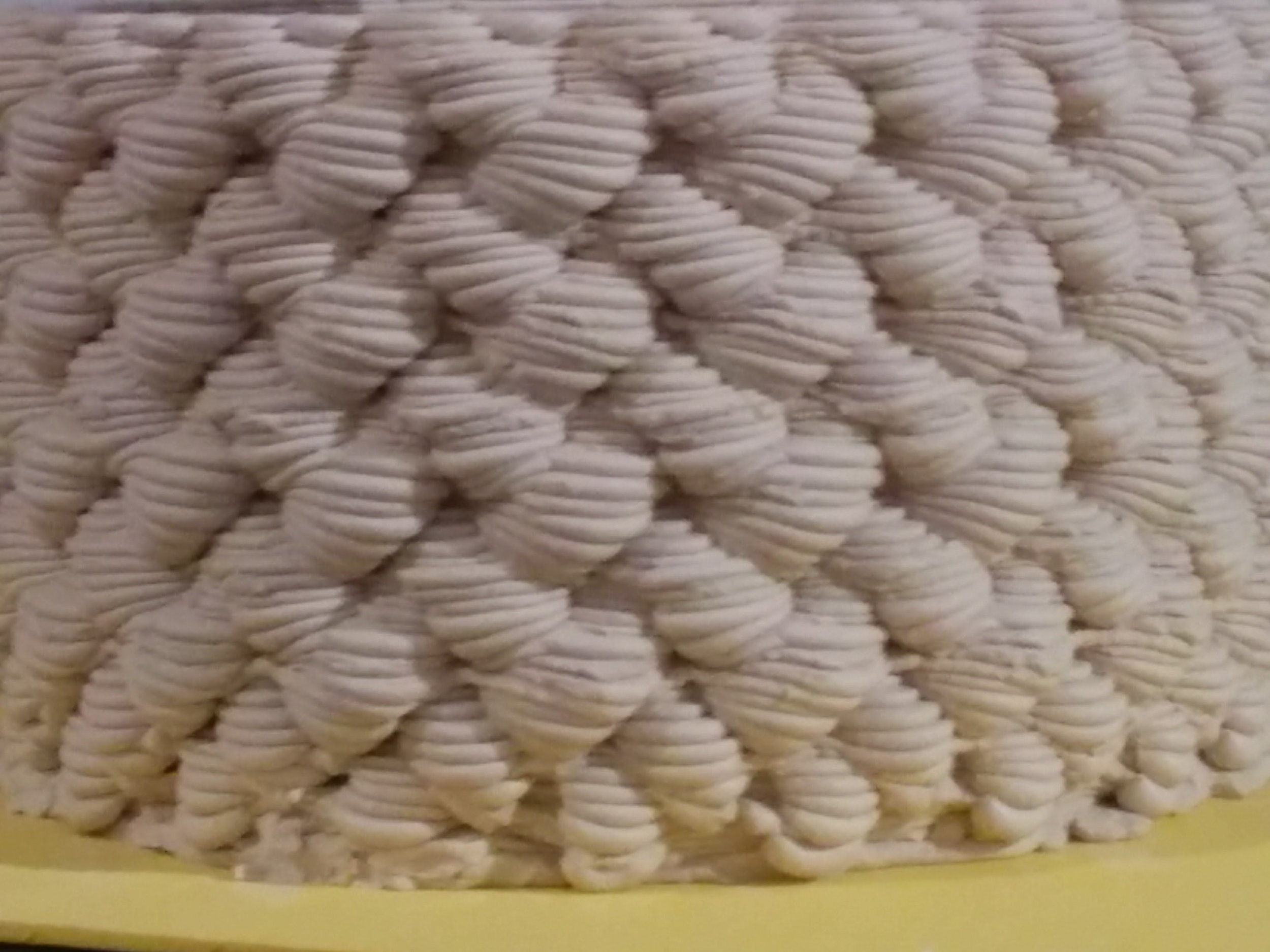
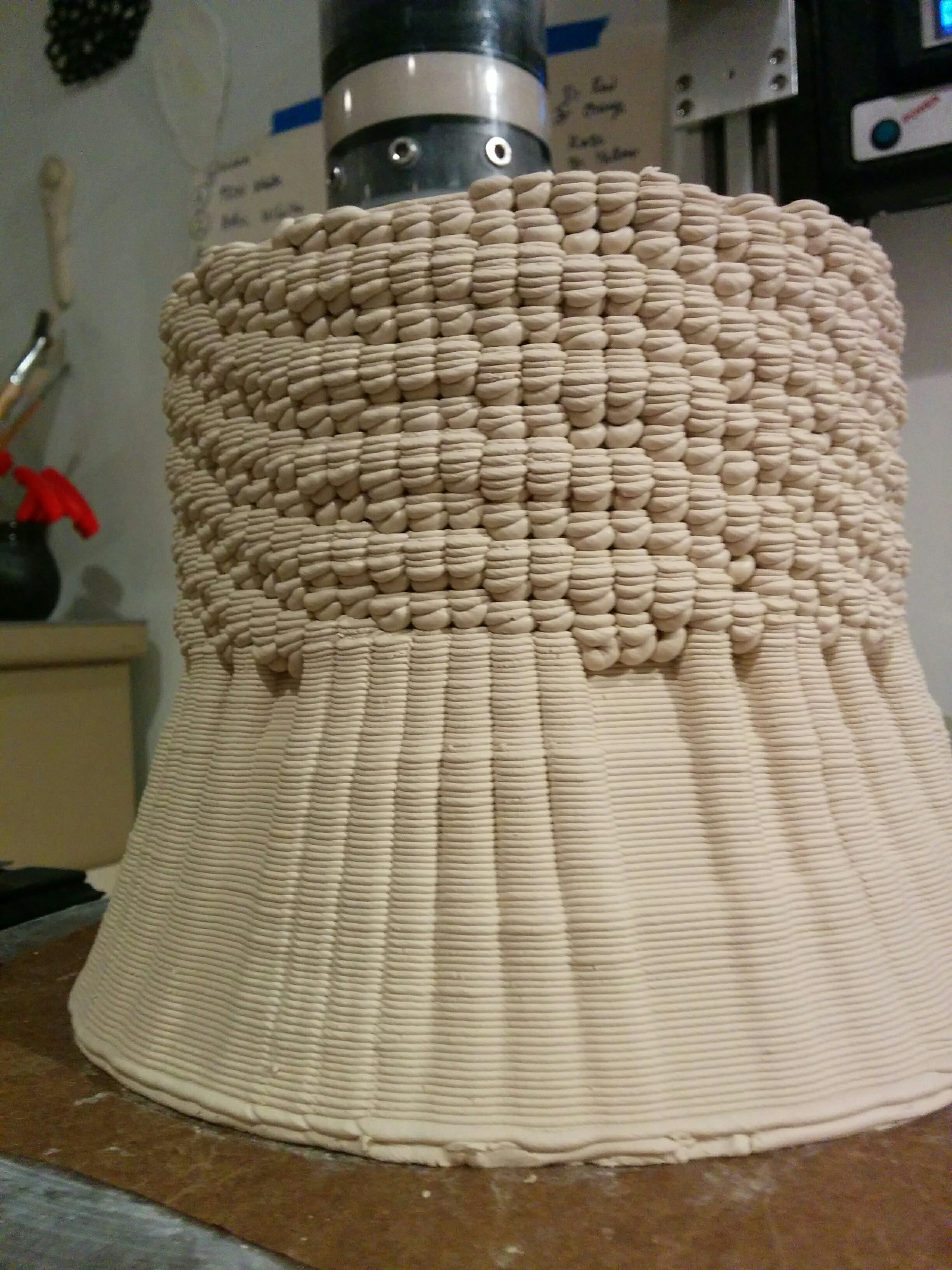
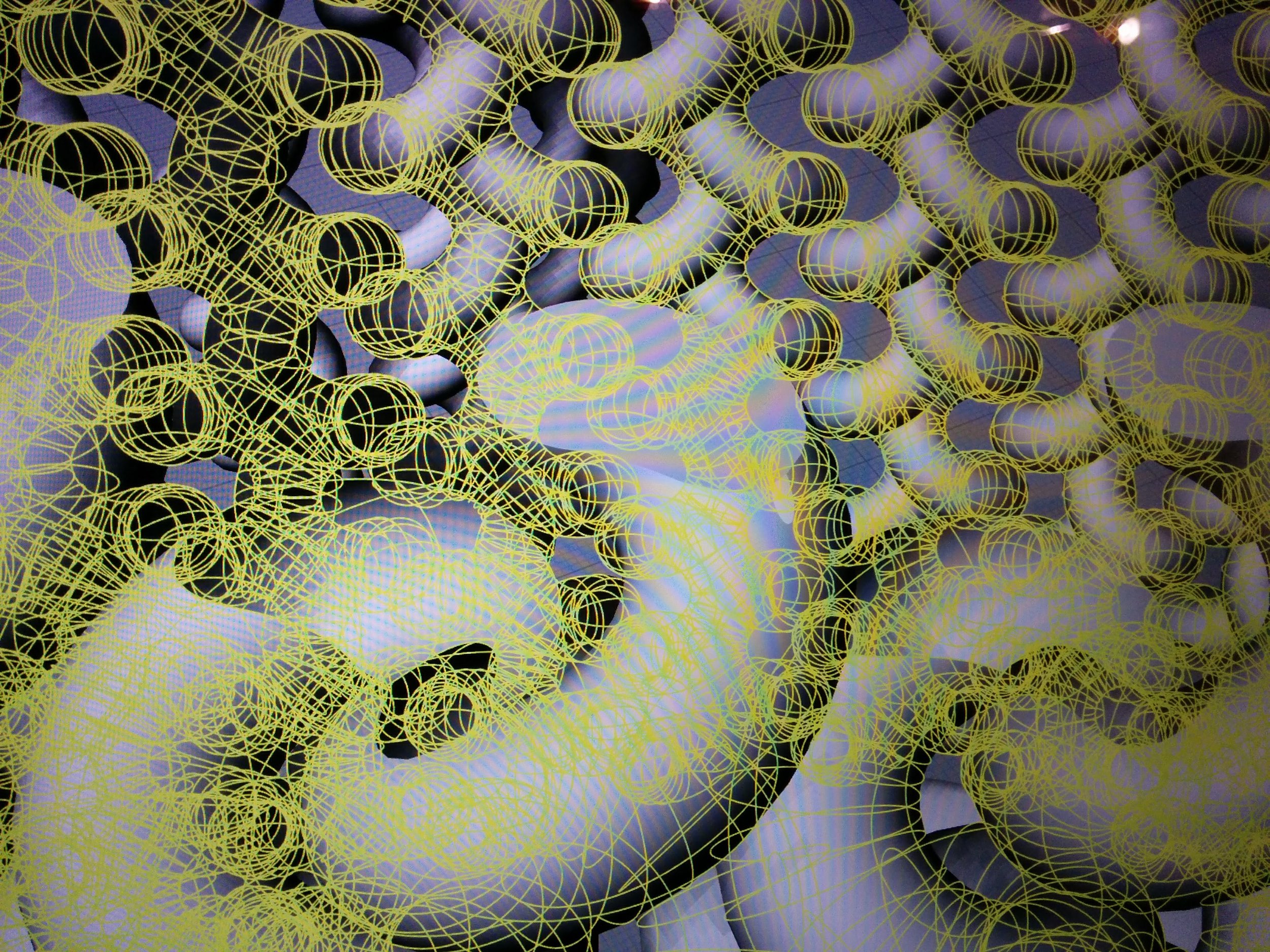
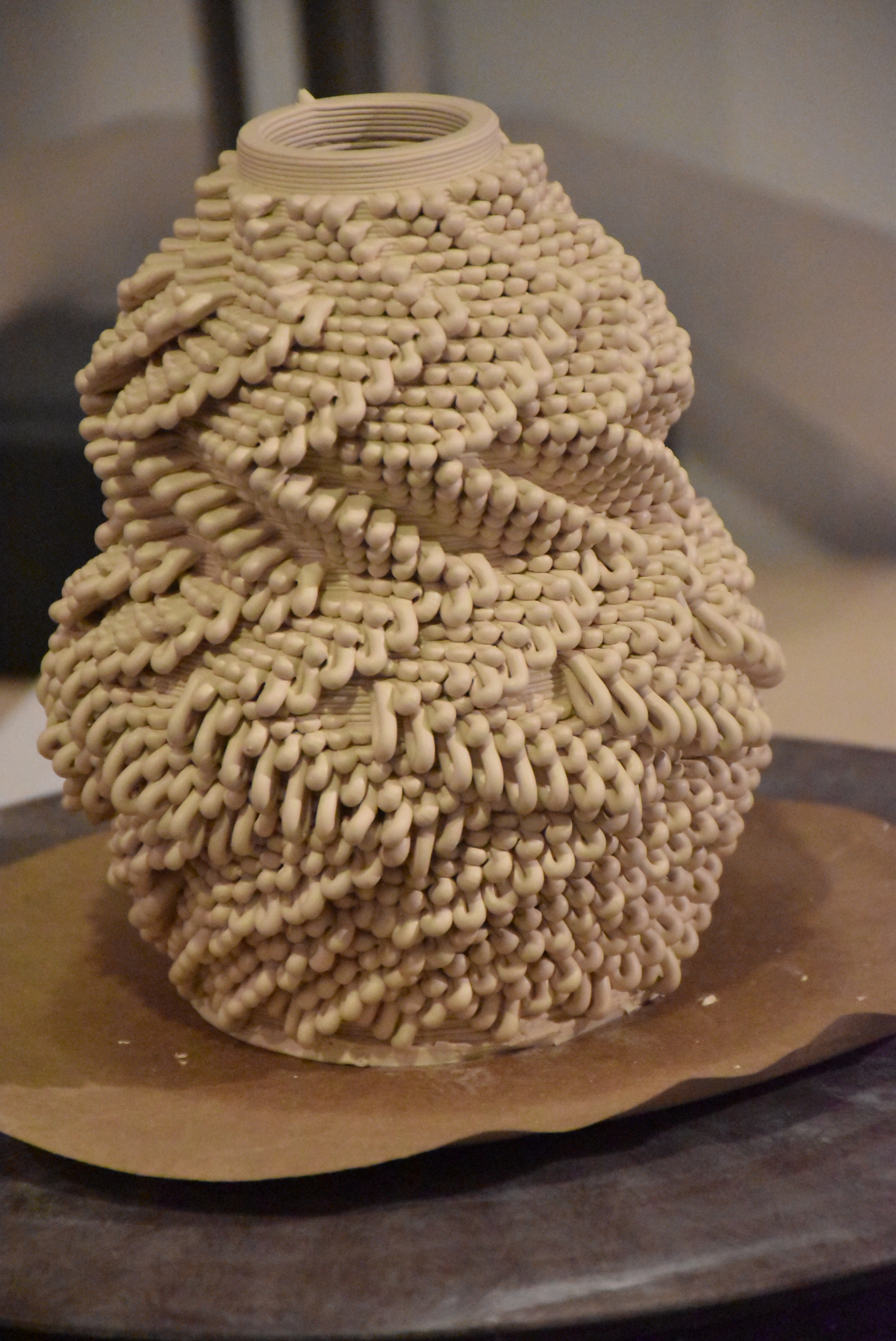
New photos of Summer Projects
Finally, we managed to wrangle a photo shoot of the larger summer projects.
Material Matters Symposium: New Craft
Silicone 3D printer made by Material Matters
On November 17th, we took a day trip to Vancouver B.C. to attend the New Craft Symposium, organized by the Material Matters Lab at Emily Carr University of Art and Design.
It was inspiring to see various projects, which expand the notion of craft into areas of design, art, fashion, technology, architecture, and social practice. The conversation about the role of makers and experimental practices of making that are in core collaborative and community oriented was equally fascinating. We came away with lots of new ideas.
Loop Tests
Slip Rabbit interns, Kate and Qing are watching the new "winged vessel" to print.
Here is a selection from our experiments using loops. Turns out, it's more difficult to make them irregular than it is to stack them in an orderly way.
Baby it's cold outside... but the kiln is on and it's 83degrees in the studio!
It's blistery and cold today. Listening to the endless drum roll of the rain while enjoying the cozy warmth coming from the direction of the kiln. We are doing the first firing of the loop tests while revisiting some of our tropical designs from the summer.
Enjoy a taste of the Slip Rabbit Tropical collection:
Inaugural Open House
On November 3rd, Slip Rabbit hosted its Inaugural Open House at the studio with lively demos and exciting discussions, an exhibition of our summer projects and, of course, food and drinks (using our studio designed cups).
Timea is explaining the process of slicing design models using Simplify3D. In the meantime, the base for Slip Rabbit's spiny vase is getting made on the printer.
Cups, cups, and more cups.... →
Fall is here and we are getting ready for the Annual Open House!
We are making a few different design prototypes for 3D printed porcelain cups. The work is a real team effort, allowing us to test and play with glaze and finish, making each cup into a one-of-a-kind, unique piece of art.
Read moreTextures galore
Possibly the most extreme texture we could come up with. Producing the "fan" design on this vessel requires very slow printing (3.5 hours) and continuous attention. It's almost like throwing on the potters wheel... constant coordination between the machine and the potter's hand.
Tech Specific Grant Support
With the help of a generous grant from 4Culture, Slip Rabbit was able to acquire two new pieces of equipment. We were excited to visit NCECA in Portland this spring and connect there with Danny Defelici, the genius behind 3D Potter, the maker of our new Potterbot 7. In addition to the 3D printer, the studio also added a 2gallon slip mixer to its arsenal, finally giving a break to the old handheld power drill.